Mike Tyson isn't known for his business wisdom. However, he could have easily been talking about industrial projects when he said of one of his opponents, "Everyone has a plan until they get punched in the face."
Even the best-laid plans for industrial projects are meaningless if the plan isn't executed properly. You may have even seen this firsthand. You spend months, maybe even years, developing a plan for your project. And then, as soon as it is time to execute the plan, something goes awry. It can be frustrating, but effectively managing surprises is one of the keys to a successful outcome.
Vendors don't always operate on your schedule, though. A vendor providing materials for a later phase task may send the shipment as soon as it's ready, much earlier than you needed. Alternatively, a vendor may miss a deadline, causing you to receive those materials days or even weeks after you were expecting.
It's especially problematic if you have limited space. You may not have room to warehouse materials and supplies that arrived early. You may not have the staff or resources to inventory and track out-of-sequence materials.
And, of course, materials arriving out of sequence could throw off your timeline. You created a specific order of events for a reason and may not be able to change the course of this task or events only because materials arrived in the incorrect order.
Fortunately, there are steps you can take to protect your timeline and ensure that your vendor shipments arrive in the order that you have specified. Below are three actions you can implement on your next industrial project:
1. Sequence, number, and track your shipments
Very often, out of sequence shipments are caused by a lack of transparency. You may have multiple shipments coming from multiple vendors. Even if you give them your desired arrival dates, there's no guarantee that they'll follow those instructions.
That's why it may be more useful to create a specific shipment plan. In that plan, you can list the exact order of deliveries and when they should arrive. Assigned numbers to each crate or shipment so you and your vendors can quickly determine where that particular shipment falls in the sequence.
Then, to gain transparency, you may want to implement scanning and tracking software. Your vendors or supply chain partner can apply barcodes to every crate, container, and shipment. As the supplies move through your supply chain, they get scanned at every step.
The data from those scans is then communicated to your software so you can track the progress of your shipments in real time. If you see that a shipment is on track to arrive earlier or later than expected, you can take action to try and correct the issue.
2. Track container contents
While it’s helpful to track the actual shipments and containers, it’s what is in those containers that’s imperative. It would be great if every vendor packaged every supply correctly. However, that's not what always happens.
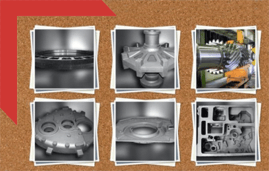
It might not be cost-effective to barcode and scan every part and material. However, you can use photo documentation software to create a digital record of what is shipped in each container.
This software records and image of everything that goes into a package or container. That image is then stored electronically in your software. Again, in real time, you can see whether certain parts and materials are making it into the correct crates and packages. If there's an issue, you can take action to resolve before it leads to bigger complications.
3. Implement a vendor management program
If you have a large, diverse network of suppliers, it can be challenging to keep them all aligned with your standards and expectations. To some degree, you have to trust that they have the processes and resources in place to meet your quality and delivery expectations.
Of course, not all vendors perform to expectations. That's why it can be helpful to have a formal vendor management program in place. In a vendor management program, you establish specific metrics, goals, and standards that you expect from each vendor. You review those metrics regularly, and if standards are being met, you look for alternatives.
A vendor management program can be especially helpful in an industrial project because it allows you to set specific expectations from the very beginning. Your vendors know your requirements, and they know what's expected of them.
You may even want to work with a supply chain or logistics third-party partner who can manage this process for you. They can manage your vendors, review performance, coordinate shipments, and packaging, and ensure that you get the shipments you need when you need them.
You don't have to be surprised by shipments arriving out of sequence your industrial project. By planning ahead and taking early action, you can ensure that your parts and materials arrive according to your project's timeline. A third-party supply chain partner who has industrial experience could be just the resource you need to implement these steps and more.
Let Us Know What You Thought about this Post.
Put your Comment Below.